Shipper | Case study
Tire manufacturer overcomes uncertainty at the port and optimizes its supply chain
Schneider Transportation Management stepped in to keep the manufacturer’s inconsistent freight moving and optimize its supply chain.
Manufacturer gains efficiencies through transportation solution
A tire manufacturer is no stranger to the importance of efficient transportation: its tires help move people and products over hundreds of thousands of miles of highway across the country. But when its primary carrier suddenly dropped its business, this manufacturer was left scrambling to figure out how it would transport raw materials from the Port of New Orleans to its manufacturing plants throughout the country. Making the situation more complex, the manufacturer’s supply chain is volatile. There is little consistency with the volume on its shipping lanes, so it wasn’t easy to find a new carrier able to adapt to fluid freight volumes.

The manufacturer needed to find a new solution for moving its freight before this disruption to its supply chain would cause delays in production. With this time-sensitive challenge in mind, the manufacturer reached out to Schneider Transportation Management for help to keep its freight moving efficiently and to optimize its supply chain.
Port logistics challenges + lean manufacturing model = complicated freight equation
Schneider led the manufacturer through the challenge of navigating port logistics and provided custom solutions that provided flexibility, scalability and innovation.
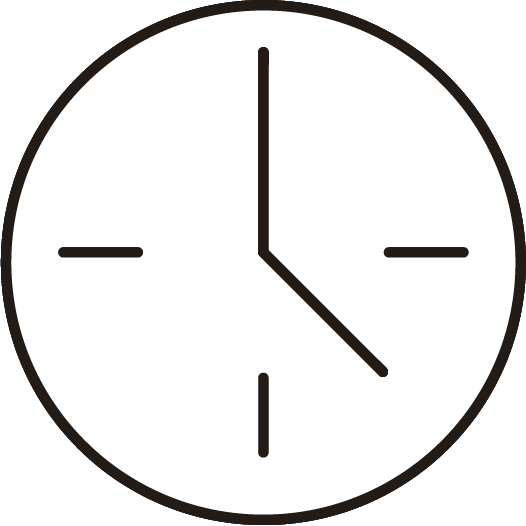
Another challenge of the manufacturer’s business was its lean manufacturing model. Because it had limited extra raw materials on hand, any delay in shipments could derail its tire production. The manufacturer was importing on average more than 40 loads per week on a number of lanes, but Schneider had less than 24 hours’ notice when a load was tendered. To secure a spot for last-minute loads and avoid disruptions in this tire supply chain, Schneider would secure capacity ahead of tender.
Unpredictable weather throws another wrench in tire supply chain
A final challenge – and one that many companies face when shipping materials to and from locations prone to extreme weather – was dealing with unexpected events impacting the supply chain. When tropical storms caused the Port of New Orleans to close, the manufacturer was forced to import its materials at a different port. To keep freight moving, Schneider was able to tap into its network of 34,000 carriers to find the capacity needed and offer a temporary solution.

Extreme weather isn’t the only unpredictable disruption that can happen to a supply chain. In 2020, the health risks of COVID-19 upended production for many manufacturers across the country. The tire manufacturer had to scale back operations. Because Schneider maintains such close relationships with its carriers through an industry-leading Carrier Purchase Program, the manufacturer didn’t have to worry that its relationships with its carriers would be harmed by the extended pause in shipments. The carriers were ready to resume shipping the manufacturer’s cargo once production resumed – and the carriers could book the freight instantly through the Schneider FreightPower® app.
Manufacturer successfully added flexibility by leveraging Schneider’s network and relationship
With the help of Schneider Transportation Management, the manufacturer avoided being left in a lurch when its original carrier backed out by implementing dynamic capacity solutions.

Schneider provided a dedicated team to care for the manufacturer’s business, providing the manufacturer with the high level of service it required to successfully navigate complicated port logistics and ship its volatile freight. In addition, a dedicated team meant that the manufacturer had a relationship with the people managing its freight and knew who to turn to with questions and concerns.
Schneider is continuing to work with the manufacturer to further optimize its supply chain and reduce costs. With Schneider’s help, the tire manufacturer is keeping its freight moving, ensuring that production isn’t delayed.
To learn how Schneider Transportation Management can create a custom solution for your tire or automotive business, contact an expert to begin the conversation.
Drive your business forward
Sign up to receive our industry leading newsletter with case studies and insights you can put to use for your business.